Fibreglass Moulds
Fiber Glass, also known as Glass reinformed Polyester (GRP) is a strong lightweight material which is less brittle than other moulds. The raw materials are also cheaper than others.
Health and Safety
-respirators
Used to filter the air you breath in to protect you from chemicals and fibres. The filters are replaced after a certain lenth of time.
-Gloves
Vinyl or Nitril gloves are most suitable as they won't react to any of the materials. Avoid latex gloves as they will, melt, burn and dissolve.
-Eye Protection
Wearing goggles with closed sides reduce the risk of any catalyst or fibres getting into eyes.
-Protective Clothing
Overalls which are loose fitting, so they can be pulled away without any skin contact.

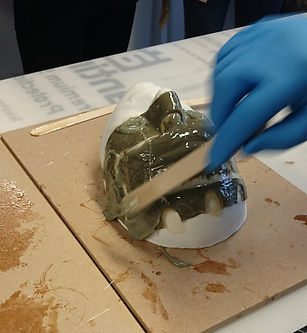


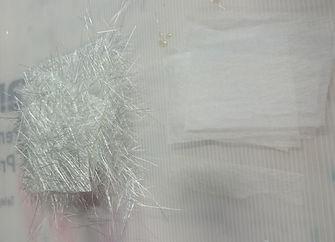
Materials
-Glass Matting
-Gel Coat Resin
-Lay-up Resin
-Fine Surface Tissue
-Catalyst
This Glass Matting is made up of long strands of glass bonded together with starch. On the right: Fine surface tissue used to make the appearance smoother and as an extra layer of strength.
Process
-Use wax mould release on core
-Mix 4.5g of catalyst with gel coat
-Used to Pick up detail/ changes colour when mixed
-Even thick coating onto clay area
-Cures slower when cold
-Should be firm and tacky after 1/2 an hour
-Lay-up REsin is Catalysed at 2% and a small amout put into a separate cup
-Make 'mud' filler paste
-use talc
-Spread filler into touchdowns
-Makes better layer to avoid trapped air
-Use a two sheet thickness of strand matting
-Using ripped smaller pieces first, wet up matting with resin first
-Overlap each piece
-Stronger bond
-Use Resin to push the matting down, untrapping air
-Repeat process
-Final layer, use fine surface tissue
-soaks up excess resin/ neat finish
.Mark on touch downs to drill
-Use drilled holes to inject materials e.g. Gelatine. 6mm drillbit
-Trim glass off upto clay edge
-To clean mould, use lighter fluid
-
-
About Materials
Glass Matting
-loose chopped strands
chopped strand matting - long strands of glass bonded with starch
-fine surface tissue (Vale)
-Fiberglass tape
-fiberglass rope
Resin
-Gel coat resin - smooth, hard polyester surface coating of a fibreglass structure
-Lay-up Resin (laminating resin) -synthetic resin
Catalyst (MEKP)
-Methyl Ethyl Ketone Peroxide - organic peroxide
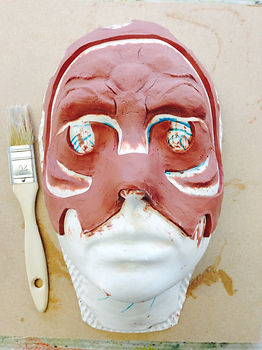

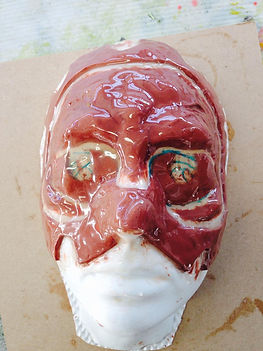


Here is my fibreglass mould I created, using the steps above. I found it difficult to stop the gel coat from building up a pool in the eye sockets, so as it started to cure, i lifted out some of it using a spatula. This made the coverage overall, an even thickness.




Using a 6mm drill bit, I drilled holes at each touchdown point whilts still atttached to the positive core.
I then prised apart the mould from the core using a chisel, then using a Oscillating saw (vibrating saw), neatened up the edges of the mould.
I then sanded this down with an orbital hand sander to remove any sharp edges, and to give a more aesthetically pleasing finish.
To clean out my mould, I used carnuba wax with a strong brush to scrub excess clay out of my mould. This would also create a layer of release, making it easier to pull appliances out of it.

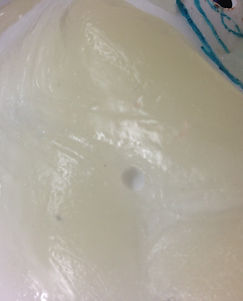

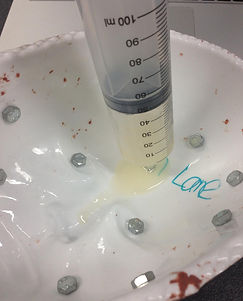

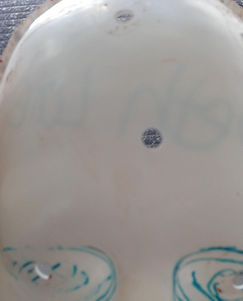


Brooks, N.2010.Mouldmaking and Casting. Crowood Press, D&N Publishing. Berkshire. Pp 99-102.129-133.
Once my mould was ready to inject, I bolted the core and the mould together, slightly loosening them to allow the gelatine to travel more freely to reach every part of my mould. I pulled up my syringe to suck up all of the melted gelatine into the syringe as I found thi eastier to reduce ari bubble risks. I then checked the syringe for air bubbles, and squeezed them out befor in jecting my mould. When injecting i ensured the syringy stayed snug in the injection hole tovoid creating an airbubble. As this rested, I tightened the bolts and left to cure.
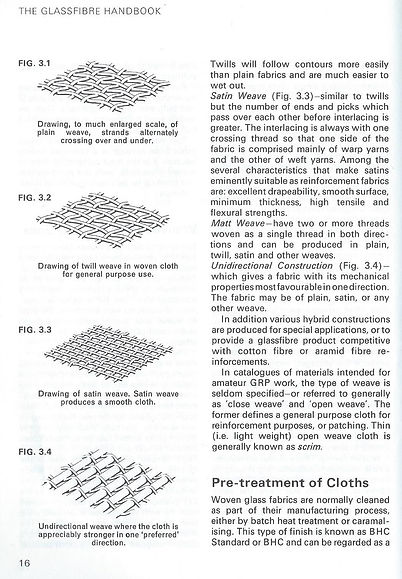
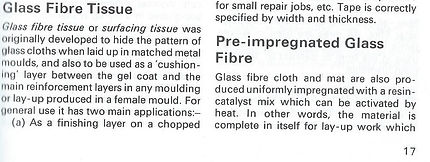



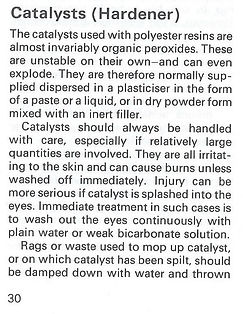


The Gel Coat resin was what I used to create my first layer.
This layes was to pick up any detail and to ensure complete coverage, especially around the grounding up when I had sculpted.
Each time I mixed up resin or gel coat, i added 2% of itf its weight of catalyst. If i added too much this could have been dangerous, resulting in a fire.
Here is an example of different lay up methods, using a variety of matting and tissue combinations.
By looking at th diagrams, you can see that some structures will be stronger than others. Thicker or closer woven strands would make a stronger layer.
Fibreglass comes in many forms. Some are chopped strand matting, and some are referred to as tissue, for finer detail. When I fibreglassed, I used surface tissue after my gel coat, this would give me a smoother surface once the fibreglass had cured. This would also make it easier to handle and look tidier as an end result.
Warring, R.H.1987 The glassfibre handbook. Swanley, Kent: Nexus Special Interests.Pp. 14-19, 22-25, 30,31, 70,71.